Guide to Supplier Quality Audits
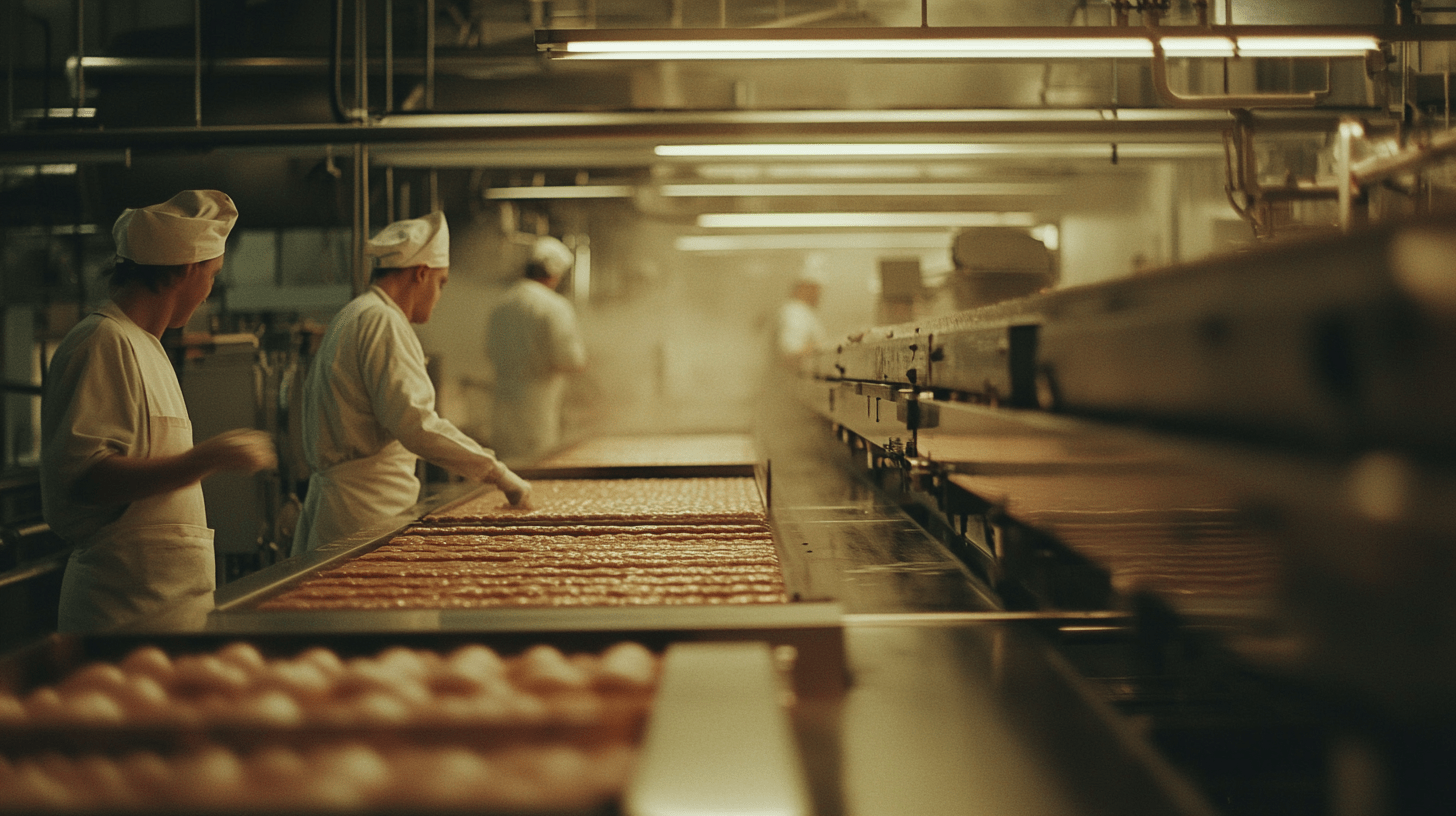
Key Takeaways:
If agility and resilience are your goals, supplier quality audits are non-negotiable.
But why exactly are they so important?
And how can you conduct them more efficiently?
These are the questions we’ll answer in this article.
By the end of it, you’ll have the tools and insights to master this critical process, proactively identify risks, and shield your organization from potential disruptions.
Let’s get into it.
A supplier quality audit is a systematic evaluation of a supplier’s processes, systems, and ability to consistently meet your quality standards for products or services.
As such, this process ensures that suppliers comply with contractual, regulatory, and company-specific requirements, protecting your organization from various risks and disruptions.
This is because quality audits provide visibility into supplier performance, which helps you address potential issues before they escalate into more serious problems.
A recent Hexagon survey highlights just how harmful these vendor quality risks can be.
As it turns out, supplier issues are behind up to half of product recalls, according to 61% of manufacturing businesses.
Illustration: Veridion / Data: ETQ
And these recalls come at a high cost.
The same survey shows that product recalls can cost companies between $8 million and $50 million.
But the damage doesn’t stop there.
Survey respondents also reported experiencing reputational damage, delayed product launches, reduced customer satisfaction, and other far-reaching consequences—all due to recalls.
Illustration: Veridion / Data: ETQ
This is exactly why quality audits are vital for any kind of business.
They give you the insight and control needed to prevent disasters like recalls or rework before they start causing significant damage to your business continuity, profitability, or reputation.
Now that you understand why thorough supplier quality audits are important, let’s take a look at some specific inefficiencies in vendor processes to watch out for.
By detecting these red flags on time, you can proactively address risks and keep your operations running smoothly.
If a supplier’s quality checks are inconsistent or poorly defined, it significantly increases the likelihood of higher defect rates in their products.
This, in turn, impacts your company through operational inefficiencies, dissatisfied customers, and potential damage to your brand reputation.
Toyota can serve as an example.
In 2010, they began carrying out stricter audits and found that some of their suppliers, responsible for producing critical components like braking systems, weren’t adhering to proper testing protocols.
Source: MotorTrend
Instead of conducting the required four tests per year, they were only performing one, putting the final product’s quality and safety at risk.
Now, the reason Toyota started to implement such strict audits in the first place was because they had a massive vehicle recall earlier that same year.
Dino Triantafyllos, their VP of North American Product Quality at the time, admitted that the whole disaster could have been prevented had they had a better auditing process from the get-go.
Illustration: Veridion / Quote: MotorTrend
The lesson here is clear: waiting for quality issues to arise before assessing a vendor’s quality control (QC) practices can be a costly mistake.
So, instead, be proactive.
Act now to make sure your suppliers’ QC processes are well-defined and effective.
Here are some key areas to focus on during your quality audits:
Documentation | Start with the basics. Review the supplier’s Standard Operating Procedures (SOPs) and work instructions to ensure their processes align with relevant standards or agreed-upon specifications. |
In-Process Controls | If possible, conduct on-site visits to confirm there are clearly defined checkpoints during production for monitoring quality. |
Staff Competence | Assess whether employees are properly trained in QC procedures. Look for certifications or documented training programs for key roles. |
Non-Conformance Handling | Examine how the supplier identifies, documents, and resolves non-conformances. |
Suppliers who check all these boxes are the ones you can trust to meet your standards consistently.
And remember: don’t wait for a crisis like Toyota’s to expose weak links in your supply chain.
Proactively audit your partners now to protect your business, your reputation, and your customers’ trust.
Non-compliance with safety standards is a serious concern with far-reaching consequences.
It can lead to accidents, injuries, or even fatalities at a supplier’s site, exposing both the supplier and the buyer to liability and reputational harm—especially if linked to a widely publicized incident.
Take it from Apple.
In 2014, they faced criticism when a labor rights group uncovered unsafe working conditions at the factory where iPhone and iPad parts were manufactured.
Source: CNET
Some of the issues found include locked safety exits, insufficient training, and a large amount of aluminum-magnesium alloy shreddings on the floor—a serious health and fire safety risk.
Kevin Slaten, former Program Coordinator at China Labor Watch, a not-for-profit organization that found these violations, accused Apple of prioritizing profits over worker safety.
Illustration: Veridion / Quote: CNET
However, it’s not just giant corporations that should worry about such issues.
Regardless of the size of your organization or the amount of exposure a safety incident could potentially receive, safety violations in a supplier’s processes should never be ignored.
Therefore, to mitigate risks, check these areas during an audit:
Regulatory and Certification Compliance | Ensure the supplier complies with local and international safety regulations. Check for certifications such as ISO 45001 or equivalent local occupational health and safety standards. |
Safety Policies and Training | See if there’s a formal safety policy. Review training records to make sure employees are trained in workplace hazards, emergency procedures, and safe equipment handling. |
Workplace Conditions | Inspect the facility for things like proper ventilation, clear, unobstructed emergency exits, and consistent use of PPE. |
Emergency Preparedness | Evaluate the availability and maintenance of emergency response systems, including fire extinguishers, first aid kits, and spill control equipment. Review records of emergency drills and procedures. |
If you encounter outdated safety equipment, inadequate emergency procedures, or non-compliance with regulations, take action immediately.
After all, addressing these issues is not just about business continuity—it’s about protecting lives.
Environmental noncompliance can lead to legal penalties or sanctions for the supplier, which can impact their operations and, by extension, their ability to deliver products or services to you.
Plus, a supplier’s environmental violations can also damage your organization’s reputation, eroding the trust of both your customers and investors alike.
Xiaomi, for instance, had to learn this the hard way.
In 2018, they faced scrutiny when prominent environmental organizations alleged that a circuit board factory in Suzhou, indirectly linked to Xiaomi, discharged copper-laced acidic wastewater.
Source: Financial Times
These findings raised significant concerns, particularly as Xiaomi was preparing for its $10 billion public offering.
According to Xiaoshu Wang, Executive Director at MSCI, a leading provider of tools and services for the global investment community, investors definitely care about your ESG performance.
Illustration: Veridion / Quote: Financial Times
And so do the customers and regulatory bodies.
So, to stay compliant, operationally stable, and aligned with stakeholder’s expectations, consider incorporating the following checks during supplier audits:
Permits and Licenses | Confirm that the supplier holds all necessary environmental permits and licenses for their operations. |
Regulatory Compliance | Review records to ensure adherence to local, national, and international environmental regulations. Investigate any history of violations or fines. |
Waste Management Practices | Assess how the supplier manages, stores, and disposes of hazardous and non-hazardous waste. Check for proper labeling, documentation, and disposal processes. |
Emissions Control | Evaluate systems for controlling air, water, and noise emissions. Confirm compliance with regulatory limits and the presence of monitoring mechanisms. |
Chemical Management | Examine how chemicals are stored, handled, and used. |
By systematically evaluating these areas, you can identify potential risks and then collaborate with suppliers to address the issues before they escalate.
At the end of the day, environmental responsibility is now a regulatory obligation, not just a passing trend.
Any instances of noncompliance can negatively affect your company, even if they originate from your suppliers and not you directly.
Poorly maintained or unhygienic facilities and equipment increase the risk of contamination or defects, leading to potential product recalls, operational disruptions, and legal problems.
This is especially true for industries with strict hygiene and maintenance standards, such as pharmaceuticals or food.
In 2012, McDonald’s found out just how much is on the line when it comes to poor supplier performance in this area.
At the time, Chinese regulators shut down their local meat supplier after a TV report revealed shocking hygiene violations, including workers picking up meat from the factory floor.
Source: Food Safety Magazine
Although McDonald’s quickly severed ties with the supplier, customer trust had already been significantly damaged, with many refusing to eat at their restaurants ever again.
Not only this, but they were now also left without a key vendor which exposed them to the risk of food shortages.
To avoid such scenarios, it’s best to include hygiene and maintenance practices evaluation during quality audits.
Key areas to inspect include:
Facility Cleanliness | Check for dust, dirt, spills, or waste buildup in production areas. Review cleaning schedules and records for adherence to standards. |
Equipment Condition | Look for visible signs of wear, corrosion, or neglect on machinery. Verify records for regular servicing, calibration, and inspections. |
Pest Control | Look for signs of pests, such as droppings or nests. Review pest control measures and their associated records. |
Waste Management | Evaluate waste management practices to ensure proper storage and disposal. |
Overall, proper maintenance of facilities and equipment is the foundation of quality operations.
If your supplier struggles with the basics like hygiene and upkeep, can they truly be a reliable long-term partner?
There’s no denying that conducting supplier audits can be time-consuming and labor-intensive, especially if you still perform them manually through spreadsheets and paper forms.
Fortunately, there are all kinds of digital tools now available that can streamline your audit processes, boost efficiency, and help you gain more accurate supplier insights.
Let’s explore some of them.
For starters, AI-driven supplier data platforms like Veridion are invaluable for obtaining fresh, detailed, and reliable vendor information.
Source: Veridion
With a global, weekly-updated database of millions of suppliers and products, Veridion ensures you get the most accurate view of your supplier landscape and stay ahead of potential risks.
For example, with Veridion you can:
Essentially, all you need to know about your suppliers is right there, at your fingertips.
Then there’s Supplier Relationship Management (SRM) Software, which is super useful for organizing your audits.
SRM software offers a unified view of each vendor, consolidating contracts, certifications, historical performance data, and communication records in one platform.
This enables auditors to easily retrieve past performance data and prior audit outcomes for easier preparation and comparison.
Many such tools (like the one below) also help build the agenda and checklists for audits based on knowledge of the supplier’s past performance, compliance, and risk profile.
Source: KodiakHub
Finally, mobile audit apps help with on-site inspections.
As you can see in the example below, they enable you to record data, capture photos, and take notes on non-conformities in real time, boosting the overall efficiency of the process.
Source: GoAudits
All in all, with these tools, quality audits don’t have to be a hassle anymore.
They are a great way to save time and effort while simultaneously improving accuracy and enabling well-informed, data-driven decisions.
While no one likes to face setbacks, a failed audit doesn’t have to spell disaster.
With a clear plan, you can tackle the issue head-on, minimize disruptions, and even strengthen your supplier relationships.
Here are the steps to mitigate a failed audit:
Source: Veridion
Start by thoroughly reviewing the audit findings to identify areas where the supplier fell short.
Prioritize these issues based on their severity and potential impact on product quality, regulatory compliance, and business operations.
Then, collaborate with the supplier to discuss the findings and create a Corrective Action Plan (CAP).
This plan should include:
But don’t just assume everything’s fixed because there’s a plan.
Monitor the vendor’s progress closely and conduct follow-up audits to confirm the supplier is sticking to the CAP.
Once the deadline has passed, decide whether you’ll continue working with the supplier.
If they meet your standards now, you can move forward with business as usual.
However, if they fail to demonstrate significant improvement, evaluate the severity of the unresolved problems.
Ask yourself:
If the vendor shows potential, consider continuing the partnership under tighter monitoring.
If not, don’t shy away from ending the relationship. Protecting your business should always come first.
Industry leaders like IKEA take a similar approach.
According to Muzadded Haye, a Sustainability Developer at IKEA, their first step is always to analyze the audit findings and work with the supplier on improvements.
Illustration: Veridion / Quote: IKEA
From there, they also conduct regular follow-ups and site visits, when necessary.
And if the supplier fixes the problem, the partnership continues—but under ongoing review.
The bottom line?
Whether you’re a global giant or a growing business, how you handle a failed audit can make all the difference.
So, address issues swiftly, communicate openly, and don’t be afraid to make hard decisions when needed.
Audits don’t have to be a headache. They can be efficient, straightforward, and even empowering.
With the right tools and a collaborative approach that prioritizes long-term partnerships, you can transform the process into a seamless experience that delivers real, actionable insights.
And once you have those insights, fixing what needs to be fixed and protecting your supply chain becomes easy—no matter what challenges come your way.