The Full Guide to Supplier Risk Assessment
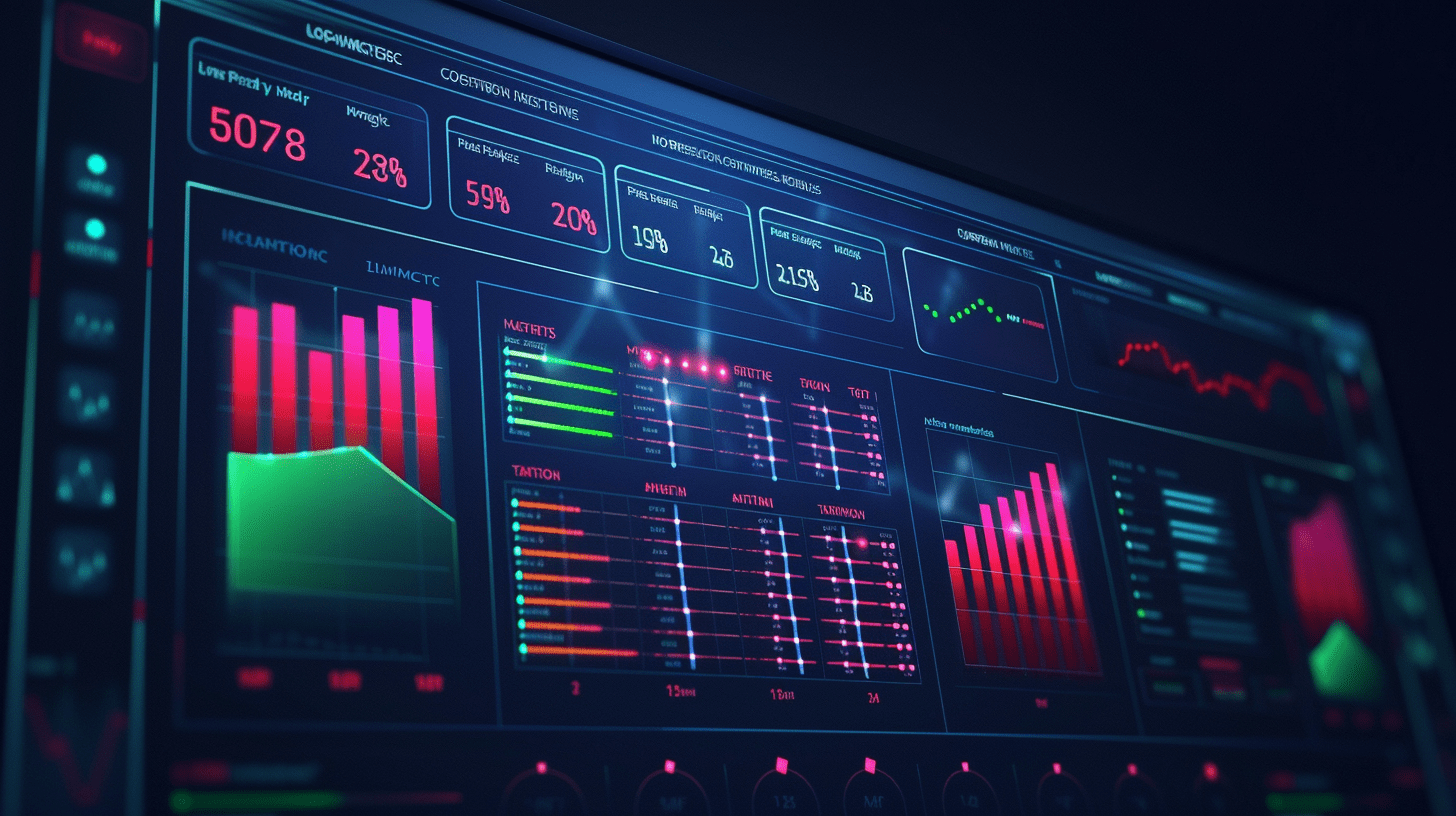
Key Takeaways:
Looking for a detailed yet easy-to-understand guide to supplier risk assessment?
Look no further.
In this article, we’ll dive deep into this essential process, covering everything from its purpose and challenges to the tools you can use to make it more efficient.
By the time you’re done reading, you’ll know everything you need to effectively evaluate supplier-related risks and navigate supply chain disruptions with confidence.
Let’s jump right in.
Supplier risk assessment is one of the key components of supplier management, aimed at ensuring the resilience of an organization’s supply chain and minimizing disruptions.
It achieves this by collecting data on various aspects of a supplier’s business operations—such as finances or ESG practices—and using this information to identify, evaluate, and manage potential risks.
The goal here isn’t to cut ties with any vendor that poses some risk.
Instead, it’s all about understanding each supplier’s risk profile and determining if it aligns with your organization’s tolerance for risk.
After all, no company is without vulnerabilities, both internal and external.
This is why supplier risk categories are so diverse, including:
Supplier risk assessment is designed to address all these categories and help protect the company from their potential impact.
And given the current volatility in global supply chains, this process has never been more important.
The findings from the 2024 Inspectorio research support this, revealing that 40% of supply chain professionals identify supply chain resilience as their number one concern.
Illustration: Veridion / Data: Inspectorio
It’s easy to see why.
Supply chain disruptions are a constant threat, taking many shapes and sizes.
For instance, a 2024 Sphera survey reports a 42% spike in supplier bankruptcies along with a 62% increase in cyber risks.
And if that’s not enough, the threat of war and geopolitical conflict is intensifying too, with related risks up by 87% in 2022 and another 7% in 2023.
Illustration: Veridion / Data: Sphera
In other words, “expect the unexpected” has become the new normal for both buyers and suppliers alike.
The purpose of supplier risk assessment is, therefore, to ensure you stay as agile as possible, minimizing the impact of any obstacle that comes your way.
Supplier risk assessment offers a range of benefits, all of which ultimately lead to stronger supply chain resilience and improved business continuity.
However, let’s go a bit deeper and explore specific gains from diligent supplier risk evaluation using some real-world examples.
First, Coca-Cola HBC demonstrates that paying attention to potential vendor risks can bolster financial stability.
They use a variety of tactics to keep tabs on suppliers’ financial health and proactively respond to any red flags.
One of these tactics is credit research.
Here’s how Coca-Cola describes this process on their website:
“Credit research provided by Moody’s Analytics includes extensive and detailed coverage on the creditworthiness of Coca-Cola HBC Critical Suppliers. This research enables us to assess risk and opportunities associated with our supply chain and develop proactively risk management programs.”
On top of that, they also use AI-powered tools to oversee the internet and social media for any developments that could impact their vendors or supply chain operations.
That way, Coca-Cola stays ahead of possible financial or performance risks, and fortifies its profitability.
Next, Boeing illustrates how risk assessment ensures consistent product quality.
Boeing uses their Supplier Quality Surveillance (SQS) program to monitor suppliers’ products and manufacturing processes for any potential issues.
Source: Boeing
They visit plants, examine supplier documents, and review every process for essentials like equipment setup, material quality, and operator expertise.
By doing this, Boeing makes sure that every part delivered meets its exacting standards, reinforcing consistent quality across the board.
Finally, IKEA shows how evaluating supplier risk can support environmental, social, and governance (ESG) goals and ensure responsible production practices.
IKEA regularly performs supplier audits to check whether they comply with their IWAY program (the IKEA way of Responsibly Procuring Products, Services, Materials, and Components).
These audits always begin with a risk assessment, helping the company identify and address potential social and environmental risks.
Stefano Bizioli Galli, Senior Sustainability Compliance Auditor at IKEA, elaborates:
Illustration: Veridion / Quote: IKEA
This allows them to find and then improve problematic areas, in turn keeping the company on track toward its sustainability goals.
All these examples perfectly illustrate why supplier risk assessment matters.
As you can see, it isn’t all about avoiding financial pitfalls (although that’s important, too).
It’s also about ensuring the organization procures top-quality products, achieves its broader goals, and builds a supply chain that’s ready to outlast disruptions and even outpace competitors.
Of course, supplier risk assessment isn’t without its challenges.
There are several factors that can complicate the process and even impact its outcomes in a negative way.
Let’s break them down.
Supplier risks are constantly evolving, often in unpredictable ways, making it complicated to identify, monitor, and analyze them effectively.
According to Tom Thimot, CEO of Supply Wisdom, a real-time risk intelligence platform, unpredictability is simply a part of today’s reality.
Illustration: Veridion / Quote: Supply & Demand Chain Executive
From regulatory changes to environmental pressures and geopolitical tensions, risks are continuously changing and intensifying, making it difficult to keep risk assessments accurate and up-to-date.
The COVID-19 pandemic is the perfect example of just how quickly and easily supplier risk landscapes can be reshaped.
Widespread factory shutdowns, labor shortages, and severe disruptions in logistics and transportation turned previously reliable partners into high-risk vendors virtually overnight.
This was far beyond what any risk assessment could have foreseen.
It’s probably no surprise then that, in a 2022 Ivalua survey, 64% of companies said ensuring supply continuity has increased in priority since COVID-19.
Illustration: Veridion / Data: Ivalua
And while the pandemic may be behind us, rapidly evolving supply chain disruptions are not.
The BCI Supply Chain Resilience Report confirms this.
As it turns out, the majority of companies (43.2%) experienced anywhere between one and five supply chain disruptions in 2023.
However, for some, this figure was much higher, ranging from 10 to a shocking 50 supply chain incidents in a single year.
Illustration: Veridion / Data: The Business Continuity Institute
The bottom line?
Supplier risks are lurking around every corner, and there’s no way to predict how they’ll evolve.
The only certainty is the uncertainty of what comes next, which makes the effective supplier risk assessment quite a difficult feat.
Even without factoring in the ever-changing nature of risks, the risk assessment process itself is complex and demanding, especially for organizations with large supplier bases.
Below, you’ll find a breakdown of all the steps involved.
Source: Veridion
Now, picture going through these steps for each supplier. It’s a massive job that can consume weeks.
In fact, according to a recent Supply Wisdom survey, 35% of companies in Europe spend five to six weeks on each supplier assessment.
Illustration: Veridion / Data: Supply Wisdom
And these assessments aren’t just a one-time task.
To keep up with changes, organizations need to reassess their suppliers multiple times a year, making this process a serious time investment.
The survey findings align with this discussion on Third Party ThinkTank, an online community where third-party risk professionals exchange insights and advice.
In the forum, members report that risk evaluations often take several weeks, due to both the complexity of the process and long wait times for suppliers to respond to surveys.
Source: Third Party ThinkTank
Sometimes, companies even need to follow up a couple of times to ensure suppliers complete their surveys.
One community member reveals another issue in the context of risk assessment complexity.
They mention that, in their company, there are multiple subject matter experts involved in the process, each conducting their own part of the assessment.
Source: Third Party ThinkTank
Performing thorough risk analysis often requires specialized knowledge in areas like financial analysis, compliance, cybersecurity, and ESG, which further complicates the process.
Overall, when you consider all the steps involved, the data complexity, and the skills requirements, it becomes clear that carrying out a thorough risk assessment is a significant undertaking.
Unfortunately, not all procurement teams have the necessary resources or expertise to perform this task effectively.
Another big hurdle in supplier risk assessment is getting trustworthy data.
This is because vendors are often hesitant to share critical information, like financials, operational details, or compliance records, due to privacy and competitive concerns.
A 2023 WTW survey backs this up, showing that 73% of organizations struggle with suppliers’ reluctance to share proprietary information.
Without this transparency, accurate risk assessment becomes almost impossible.
In fact, 77% of companies in the same survey admitted they lack the data and insight needed to understand their risks.
Illustration: Veridion / Data: WTW
And even when vendors do provide information, verifying its accuracy and authenticity isn’t always easy.
After all, supplier self-reporting can be biased or incomplete.
Third-party audits can be helpful, but also costly or difficult to arrange, particularly if the supplier operates in a remote or high-risk area.
As a result, many organizations are left relying on incomplete or potentially unreliable data, which means they can’t be fully certain who their suppliers really are and how they operate.
Jenna Wells, Chief Customer & Product Officer at Supply Wisdom, aptly summarizes the core of this problem:
Illustration: Veridion / Quote: Supply Wisdom
At the end of the day, supplier data is the lifeblood of effective risk assessment.
Without it—or without the ability to confirm its accuracy—any insights derived from this information may be incomplete or even misleading, potentially doing more harm than good.
Fortunately, most of these challenges can be addressed with the right supplier risk assessment tools.
In this article, we’ll highlight two of the most effective ones.
First up is Supplier Relationship Management (SRM) software.
Think of it as your command center for supplier management: it not only tracks every interaction with your suppliers but also gives you a full 360° view of their performance.
This includes quality, delivery, financial stability, collaboration, innovation, sustainability, and all sorts of other metrics.
For example, the SRM solution below offers detailed insights into a supplier’s financial health.
Source: Kodiak Hub
It provides ratings on the probability of default, credit limits, profitability, solvency, and liquidity, all consolidated into a clear credit score.
Moreover, SRM systems often come equipped with supplier scorecard features that allow you to centralize all that you know about your suppliers’ performance and evaluate them at a glance.
You can even customize supplier-specific rating schemes based on your risk tolerance, and receive automated updates on changes to supplier risk levels.
With SRM software, supplier risk assessment doesn’t have to be so complex anymore.
Another valuable tool to consider is supplier data platforms, especially those powered by AI, like Veridion.
Remember how we mentioned that tracking down reliable supplier data can be extremely difficult?
With Veridion, that finally changes.
Leveraging cutting-edge AI, Veridion scans the internet weekly to deliver fresh, accurate insights about suppliers, their products, ESG practices, and other vital information.
Source: Veridion
This enables you to spot any changes in a supplier’s business activity before they impact you.
For example, Veridion allows you to check a company’s worker safety and labor law compliance, which helps you ensure you work only with operationally stable partners.
Moreover, with Veridion’s detailed location insights, you can analyze your vendors’ geographical distribution to identify regional risks such as political instability, sanctions, or environmental challenges.
Plus, our solution even sends you real-time notifications as soon as it detects supplier risk, such as, for example, bankruptcy, empowering you to proactively tackle any issues that come your way.
Source: Veridion
In short, Veridion always keeps you in the loop and one step ahead—no matter how unpredictable the market gets.
Congratulations!
You’re now set to level up your supplier risk assessments, empowering your organization to stay agile and tackle supply chain challenges head-on.
To put what you’ve learned into action, start by focusing on your most critical suppliers.
There’s no need to overwhelm yourself from the get-go and assess every single supplier you work with.
Instead, identify the ones that matter most, define your criteria and risk tolerance, and start evaluating them.
You’ve got this!